| Oil Mopping Project |
Hydrographic Surveys Completes Submerged Oil Dragging
Procedure
March 2, 2005
Sewell, NJ - Hydrographic
Surveys has recently completed "mopping" operations at two ship berths on
the Delaware River
using specifications provided by
the New Jersey Department of Environmental Protection. Having developed a
comprehensive
procedure and a combination of
custom fabricated and off-the shelf-materials, Hydrographic Surveys was able
to certify two
ship berths as free of residual
oil deposits for upcoming dredge projects.
The Submerged Oil Dragging
Procedure was developed by NJDEP in response to concerns about dredge
materials possibly
becoming contaminated with
residual oil deposits from the November 2004 oil spill on the Delaware
River. The procedure calls
for dragging viscous snare
material over the top of sediments in the proposed dredge area. This
material is gathered in small
bundles called ‘pompoms’ and
attached to a weighted beam which is then submerged to contact the bottom.
The beam is held
perpendicular to the direction of
travel, such that a continuous area of coverage the length of the beam is
created. After each pass
of the mopping beam, it is raised
and inspected for any trace of residual oil deposits. Photographs are taken
and the condition of
the sorbent materials are recorded.
If residual oil is detected, the contaminated materials are removed and
replaced with new
‘pom-poms’ and the procedure is
repeated until no oil is detected.
Hydrographic Surveys responded to
a request on February 24, 2005 by Weston Solutions, of West Chester, PA, to
provide a
towing vessel and all associated
equipment to complete "mopping" work on the Delaware River. In just five
days from notification,
using resources and expertise
related to similar projects, Hydrographic Surveys was prepared to complete
the work on
March 1, 2005. Some of the
hurdles which had to be overcome to complete this task included redeploying
the survey vessel
‘Michele Jeanne’ from Elizabeth,
NJ to Gloucester, NJ, developing a comprehensive operations and safety plan,
and fabricating the
beam and necessary components for
lifting and dragging operations.
Submerged Oil Dragging Procedure – Delaware
River Berths
Time Requirement
•
Dragging must begin at most 2 weeks
prior to the dredging operations unless special circumstances such as vessel
traffic or
weather prevent commencement in which case, specific permission
must be obtained from NJDEP.
General
Description:
•
Prior to dredging, a dragging of sorbent
material atop sediments to detect residual oil deposits from the November,
2004 oil spill.
•
A towing vessel dragging a weighted
mopping beam aligned perpendicular to the direction of travel.
•
Towing vessel traveling along parallel
transects within the area to be dredged using a DGPS navigation system with
data logger
accurate to +/- 1 meter.
•
Sorbent pom-poms in sufficient number,
attached to the mopping beam to ensure continuous coverage along the mopping
beam.
•
Towing cables or chains of adequate
strength and length to ensure the mopping beam remains in contact with the
river bottom
during dragging.
Performance
Criteria
•
The dragging vessel shall proceed at no
more than five (5) knots.
•
At a minimum, the transect spacing
should be as wide as the towing vessel’s mopping beam such that there is a
reasonable
attempt to make contact with all areas
to be dredged.
•
The mopping beam transects should extend
so mopping occurs at least 25’ outside of the area to be dredged, if
accessible.
•
After each pass, the mopping beam shall
be completely removed from the water and inspected.
•
The condition of the pom-poms (no oil,
lightly oiled, heavily oiled) and type of oil (black oil, medium/#2 oil or
light oil), if
encountered, shall be noted for
inclusion in the Field Report.
•
Photos will be taken when oil is present
and/or before the pom-poms are discarded.
•
If oil is encountered, clean pom-poms
shall be attached and the same transect path shall be dragged again to
determine if oil has
been removed or if additional oil
is present.
•
If significant operational hindrances
are encountered due to trash, debris, or other unforeseen physical
obstacles, environmental
or time constraints, the
operation can be modified in the field to adapt to these hindrances,
including modifications to transect
spacing and coverage area as long
as a diligent and reasonable effort is made to "mop" the greatest area
possible under the given
conditions.
Data Logging and
Field Report should include:
•
Berth name and date(s) of dragging
operations.
•
Time of each transect run and an index
number assigned to each transect run.
•
Description of the condition of the
pom-poms correlated with each transect run.
•
Photos of pom-poms will be included in
Report and correlated to respective transect run.
•
An AutoCAD drawing (or equivalent) of
the berthing area including major features (piers, bulkheads).
•
The recorded vessel position at a
minimum of 5’ intervals along traveled field transects as recorded by the
vessel’s electronic
positioning system, including the
corresponding depth. Transects indexed as referenced in the Field Report.
•
Signature of the person with
responsibility for the dragging operation to include a statement as to the
integrity of the Report
•
Field Report Submitted to NJDEP Office
of Dredging and Sediment Technology.
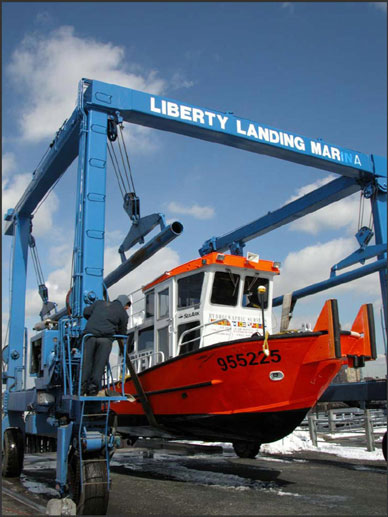
Preparing to
Re-Deploy
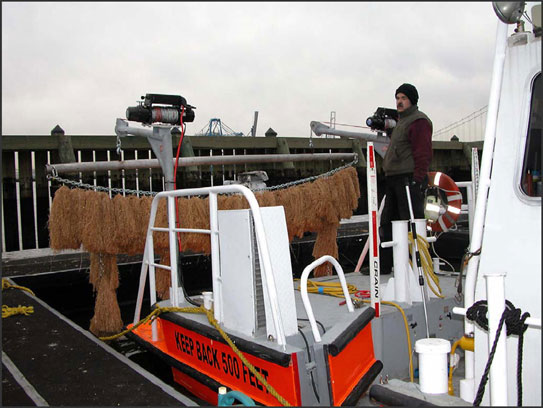
Completing
installation of winches and lifting tackle at Riverside Marina,
Gloucester, NJ.
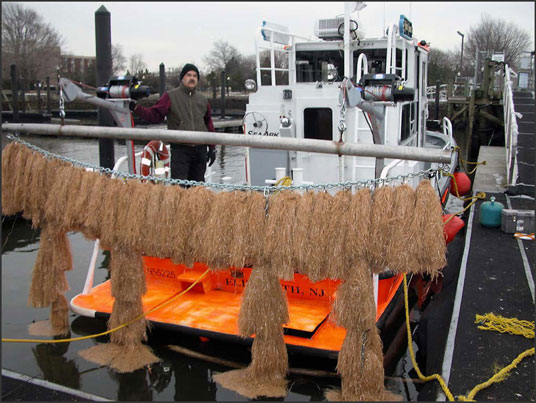
Completed rigging and dragging bar, with
viscous snare material attached.
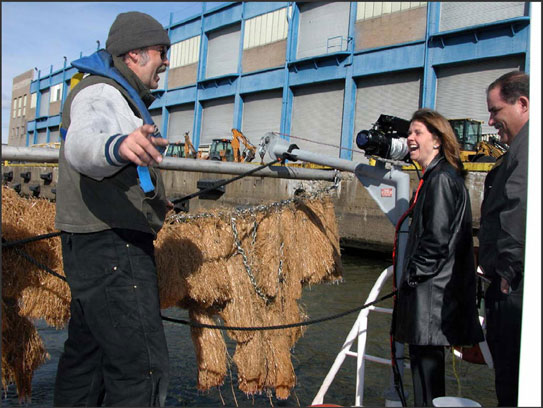
Explaining
methods and procedures to representatives of Philadelphia Regional Port
Authority.
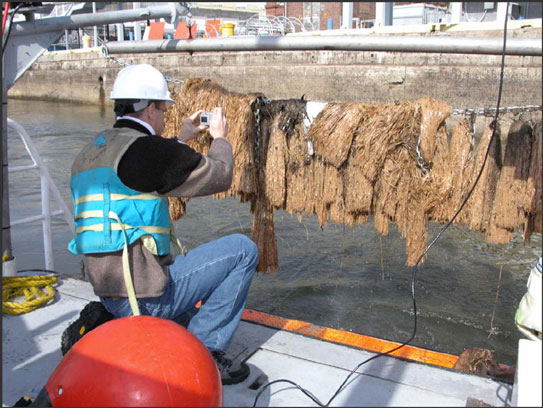
Condition of
viscous snare material being documented after each pass.
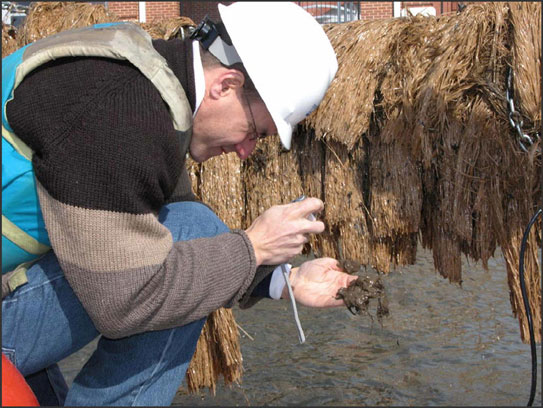
Sonny Rutkowski, Weston Solutions,
examines and photographs sediment from mopping.
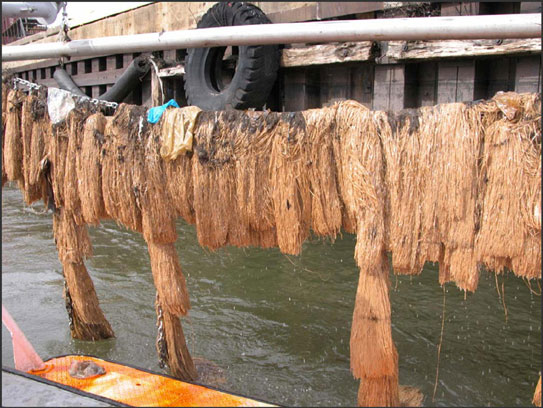
Typical Sediment and Debris, no oil
present.
|